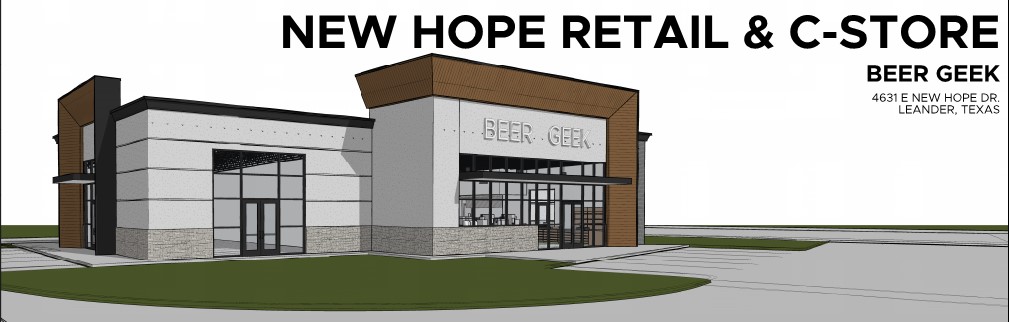
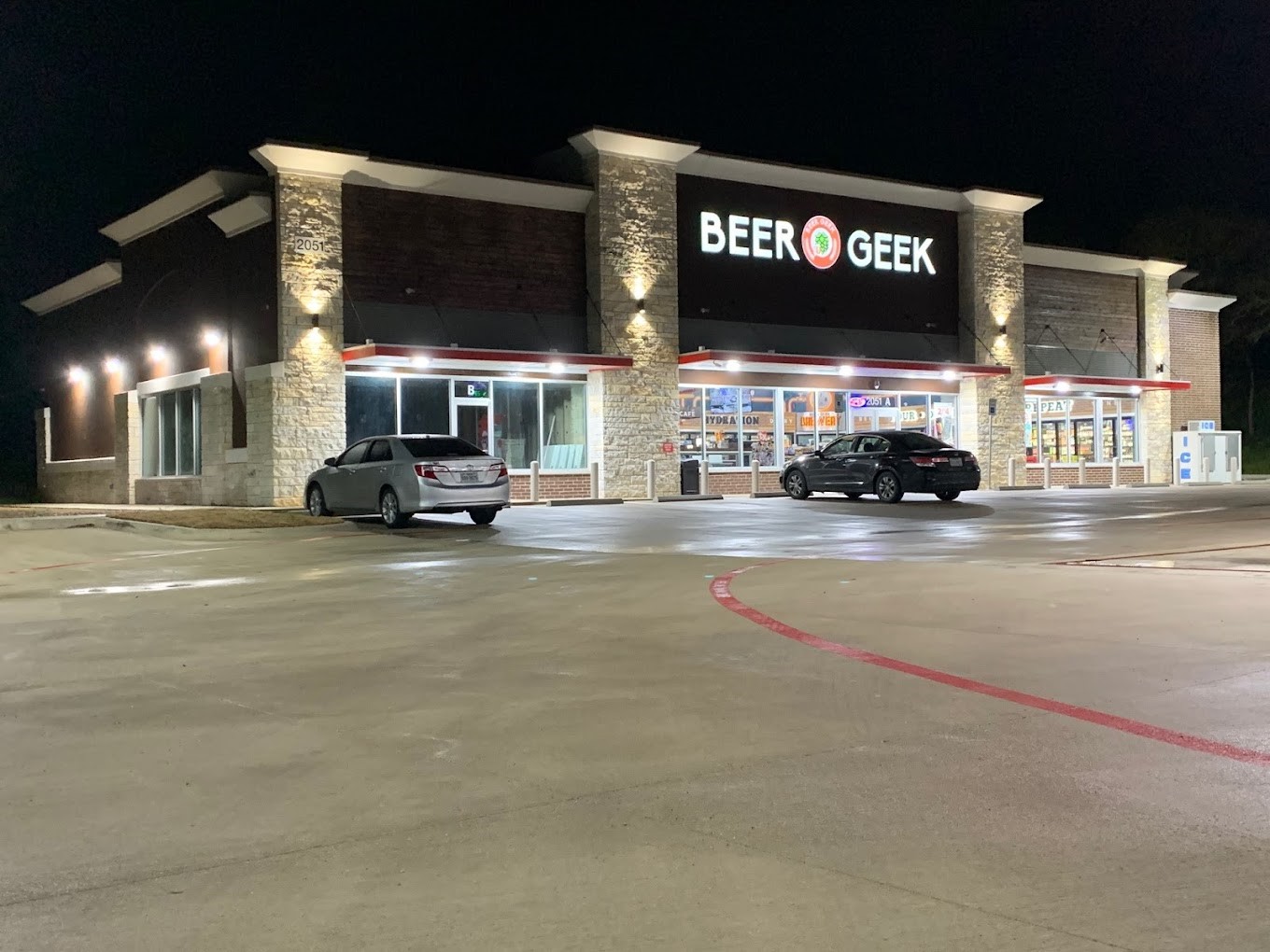
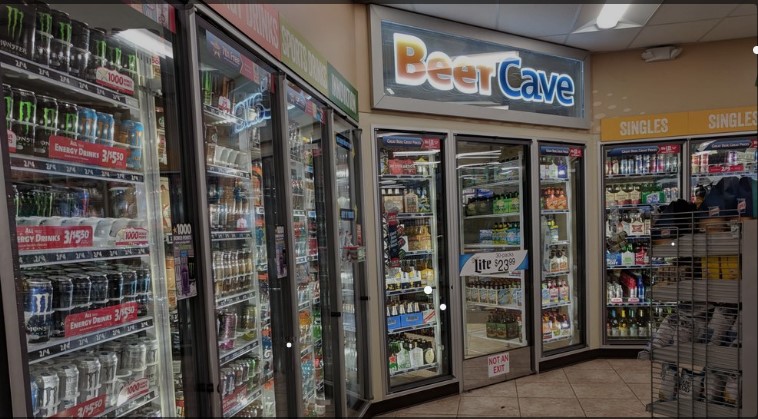
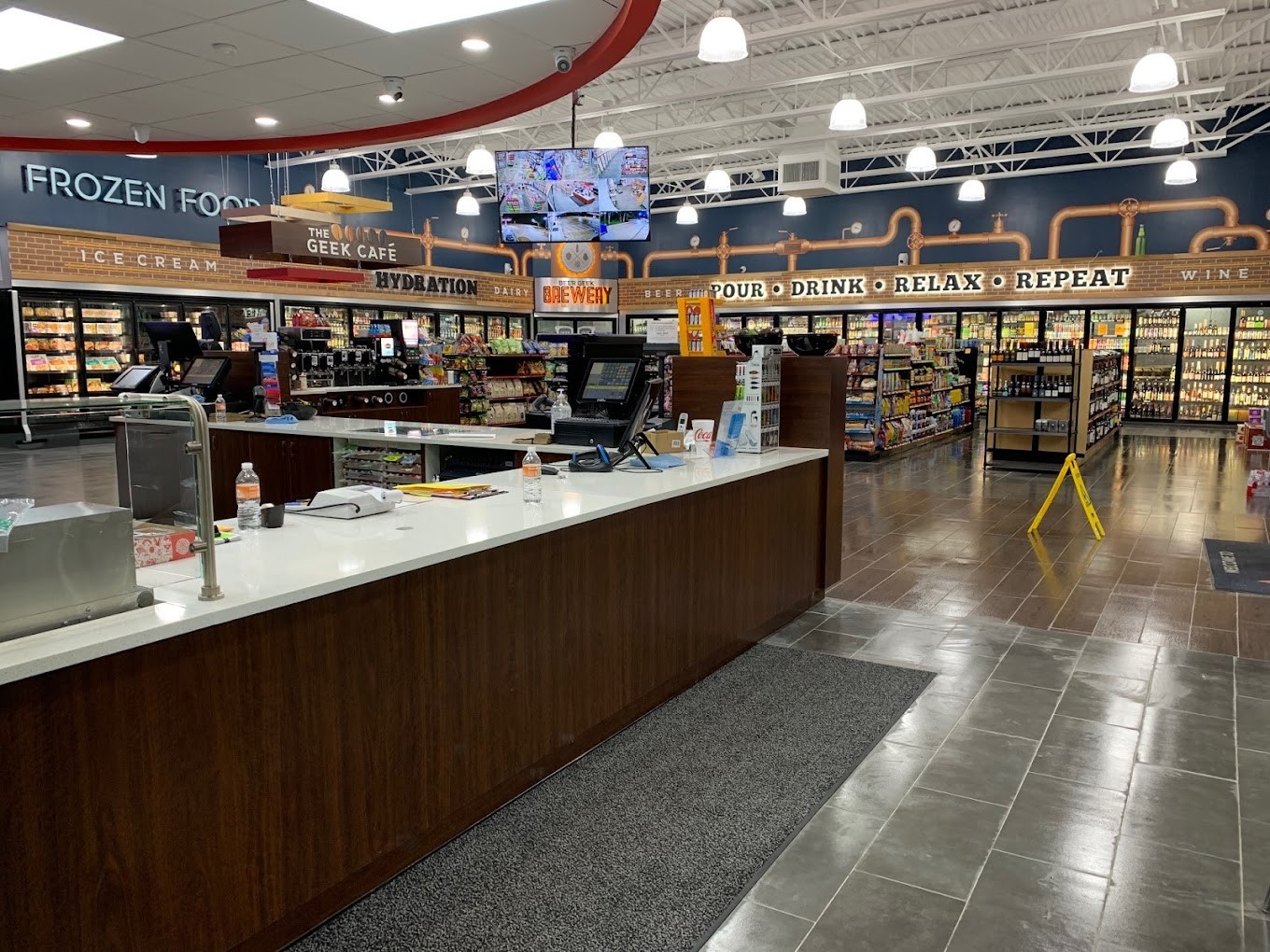
NEW HOPE RETAIL & C-STORE, LEANDER, TEXAS
Balancing multiple cooling, air pressure needs in a combination commercial space
Location: Leander, Texas
Services: Mechanical, electrical, and plumbing
Category: Convenience store
Area: 5,300 sq. ft.
Software: AutoCAD, COMcheck, HAP 5.11, McQuay Duct & Pipe sizers
The New Hope store is a popular convenience store equipped with coolers, freezers, and a commercial kitchen. One mechanical challenge for 3S MEP + Structural was balancing two key cooling loads: heat generated by kitchen equipment and infiltration from the frequent opening of the store doors.
To address this infiltration, 3S engineers designed a system to create negative pressure in the kitchen, to prevent kitchen air from escaping, and positive pressure in the store, to minimize outside air entering.
The retail design required maintaining optimal temperatures for different areas in the store and the wide range of products they cook and sell.
In the kitchen, the exhaust hood and makeup air system were specifically designed to handle the heat output of ranges, fryers, and other equipment, and the air balance was calculated to ensure proper pressurization throughout the space.
Selecting the right equipment, such as rooftop units and exhaust fans, was crucial for efficient operation.
The electrical design included a lighting layout and power distribution plan to accommodate the different needs in the various spaces. This required dedicated circuits for refrigerated shelves, produce section coolers, and other equipment that uses specialized power.
The plumbing design encompassed both domestic water supply and sanitary waste disposal. The team also selected a gas water heater and a grease interceptor.
Grease interceptors are mandated by health departments (reference codes like IPC or NPDES) for commercial kitchens exceeding a specific FOG threshold. These devices prevent sewer blockages and FOG discharge into waterways, protecting public health and the environment. For the grease interceptor, we chose a 90-day cycle.
With all 3S MEP projects, a primary focus is integrating MEP and structural designs with the construction and architectural partners and the end-users to minimize the need for design adjustments or revisions during the construction process. Design teams from 3S MEP actively engage with all stakeholders to identify potential conflicts and optimize overall system layout. Our teams are exceptionally proficient at harmonizing essential building elements for successful outcomes.